- FGD nozzle,
- 120° FGD spary nozzle,
- 90° FGD spary nozzle,
- 110° FGD spary nozzle,
- Flue gas desulfurization nozzle,
- FGD Absorber slurry spray nozzles,
- LIME LIMESTONE SLURRY FGD nozzles,
- silicon carbide Spray nozzle,
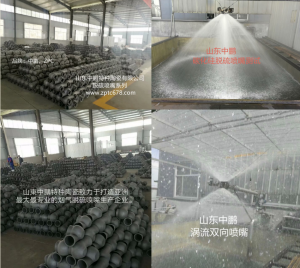
For the wet desulphurisation of flue gas, it is passed through an absorber (scrubber). The lime suspension offered in the absorber (limestone or lime milk) reacts with the sulphur dioxide from the flue gas. The better the mass transfer, the more effective the desulphurisation is. Simultaneously with the absorption, the flue gas is saturated with water vapour. The so-called "clean gas" is usually discharged via a wet chimney or cooling tower. The water thus lost for the process must be replaced. The lime slurry pumped in circulation is kept chemically active by repeatedly draining a saturated partial flow and replacing it with new reactive suspension. The drained part flow contains gypsum, which – simplified – is a reaction product of lime and sulphur and can be marketed after dewatering (e.g. for gypsum walls in the construction industry). Special ceramic nozzles are used to inject the lime suspension into the absorber. These nozzles form many small droplets from the pumped suspension and thus a correspondingly large reaction surface for good mass transfer. The ceramic material permits long service life despite the fact that lime suspension with gypsum content has abrasive properties. In the design we attach great importance to free cross-sections, so that smaller impurities in the suspension cannot set the nozzles. For economical operation, these nozzles can be adapted to the highest efficiency range of the pump. A nozzle can be specified for (almost) every process engineering challenge. In addition to full-cone and hollow-cone nozzles in various spray angles and flow rates, the ZPC nozzle with patented twist compensation is also available. The absorption zone consists of several levels of nozzles and a horizontally installed droplet separator system, in order to return the fine droplets carried along in the gas stream to the process. With our high performance droplet separators you can increase the efficiency of your plant. The solids in the suspension can lead to deposits, e.g. in the droplet separator, in the inlet duct or on pipes, which can lead to problems in operation. Since water is always withdrawn from the circuit through evaporation, water must be fed into the absorber, which can and should be used for cleaning. ZPC tongue nozzles have proven themselves for cleaning the flue gas inlet. ZPC full cone nozzles are usually used for cleaning the droplet separators. Plastics (e.g. for pipelines) and rubber (e.g. gaskets, rubber linings, etc.) are often used in an absorber whose temperature resistance is lower than the temperature of the uncooled flue gas. Normally, the suspension pumped in a circuit cools the flue gas sufficiently, but if, for example, the feed pump is suspended, the plastics and rubbers could be destroyed. Small special-alloy metal nozzles have proven their worth here, which take over cooling during this time and thus protect the investment of the flue gas desulphurisation plant.
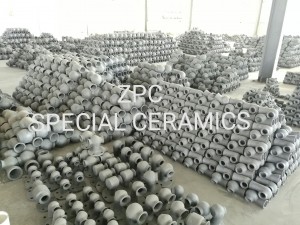